模压成型工艺过程包括:嵌件放置并预热、加料、合模、排气、保压、固化、脱模、清理模具等步骤,接下来就给大家详细介绍一下各个步骤。
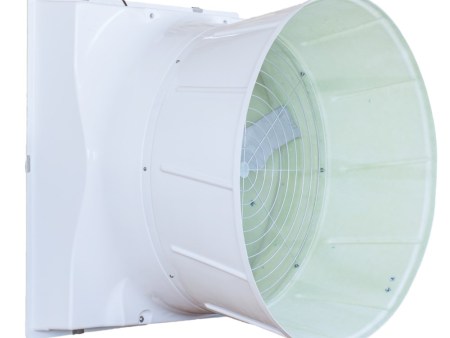
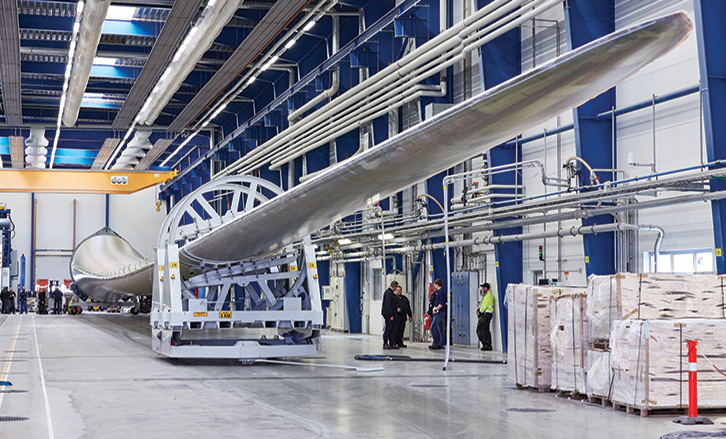
嵌件一般由金属制成,可对制品起增强作用, 使用嵌件的制品力学性能提高较大。也有的是为了给制品赋予导电、导热特性或者其他功能特性而加入嵌体。嵌件放置前,进行预热为佳。
通常是用手放置嵌件,放置位置要准确、稳定,若是小型嵌件亦可用钳子或镊子安装。一件制品可以用一个嵌件,也可放置几种不同的嵌件,其位置不得放错,不得歪斜,一定要使嵌件稳定,必要时应加以固定,防止位移或脱掉,否则达不到使用嵌件的目的,反而会造成制品的报废,甚至会损害模具。
加料量的精确度会直接影响制品的尺寸与密度,应严格加以定量,将物料均匀地加入型模槽中。定量加料法有:重量法、计数法和容量法。
重量法准确但较麻烦,多用于尺寸要求精确和难以用容量法加料的物料,如碎屑状、纤维状物料。
容量法不如重量法准确,但操作方便,一般用于粉料计量。
计数法只用于预压物料加料。
注意事项:加料前,应首先检查型腔内是否有油污、飞边、碎屑和其他异物。将准确计量的物料, 按型腔形状加入,对某些流动阻力大的部位应尽可能填满,并注意难以充模部位(如凸台、细小孔眼、狭缝及开口附近),应多加些物料。为了排气方便,最好将物料中间突起,并在嵌件周围预先放上物料并压紧,这样可减少料流对嵌件的冲击力,嵌件的插孔内也不会发生“逃料” 现象。如果预先预压成制品形状加料更为方便。
合模分为两步,凸模未接触物料前,需低压(1.5 一 3.0MPa)快速,这样,可以缩短周期和避免塑料发生变化,当凸模接触物料之后,应开始放慢闭模速度,改用高压(15-30MPa)慢速,以免损坏嵌件、并使模内空气排出。
为了排除模内空气、水气及挥发物,在模具闭合后,有的还需要将模具开启一段时间,这个过程称为排气。排气操作应力求迅速,一定要在物料尚未塑化时完成。否则物料硬化而失去可塑性,此时即使打开模具也排不了气,即使提高温度和压力也不可能得到理想的制品。排气可以缩短固化时间,而且能提高制品的力学性能和电性能。为了避免制品的分层现象,排气过早过迟都不好,过早达不到排气的目的,过迟物料表面已固化,气体排不出来。
物料从流动态变成坚硬的不熔不溶状态的过程称为热固性树脂的固化。这里所讲的固化实质上是讲固化速度,即变定速度,它是在模压标准试样时,塑料在模具内变为不熔不溶状态时的速度,通常都用(s/cm厚度)来表示。固化速度与塑料的性质、预压、预热、压制温度和压力等因素有密切的关系。
固化速度的快慢取决于树脂中低相对分子质量组成向高相对分子质量产物转化的速率,即固化速度与树脂的分子结构有关。如:热塑性酚醛树脂因相对分子质量较低,支链少,固化剂容易与活泼基团反应,所以硬化速度快。相对分子质量高, 粘度越大,不利于活泼基团(羟甲基)的缩合,因此固化速度慢。固化速度的快慢直接影响到生产效率。为了加速热固性塑料的固化,有时在成型时加入一些固化剂, 如热固性酚醛模塑粉可加入六次甲基四胺;脲醛模塑粉可加入草酸等固化剂。某些无机填料对模塑粉的固化速度也有一定的影响,如镁的氯化物或氢氧化物便能加速酚醛模塑粉的硬化。
树脂在模内固化的过程始终处于高温和高压之下,从开始升温、加压、到固化至降温降压所需要的时间称为保压时间。保压时间实质上就是保持温度和压力的时间,它与固化速度完全一致,保压时间过短,即过早地降温降压,会导致树脂固化不完全,降低制品的力学性能和电性能以及耐热性能。同时制品在脱模后会继续收缩而出现翘曲现象。保压时间过长,不仅延长生产周期,而且使树脂交联过大,导致物料收缩过大,密度增加,树脂与填料之间还会产生内应力,严重时会使制品破裂。因此,必须根据塑料性能制定适当的保压时间,过长过短均不适宜,通常在模压时将固化时间调节在 30s 到几分钟不等。
脱模通常是靠顶(出)杆来完成的。带有成型杆或某些嵌件的制品应先用专门的工具将成型杆等拧脱,而后再进行脱模。
由于模压时可能在模具里留有一些残存的物料及掉入飞边。所以每次模压后必须将模具清理干净,如果模具上附着物太牢可以用铜片清理,也可用抛光剂拭刷等,清理后涂上脱模剂以便进行下一次模压。
为了进一步提高制品的质量,制品脱模后,常需在较高温度下进行处理,后处理温度的高低视塑料的种类而异。后处理的目的是:
①保证塑料制品固化完全。
②减少制品的水分及挥发物, 以提高其电性能。
上一篇:AIRTECH隔离膜 常规尺寸
下一篇:船体真空导流一体成型工艺(操作讲解)