Composite Tooling Materials
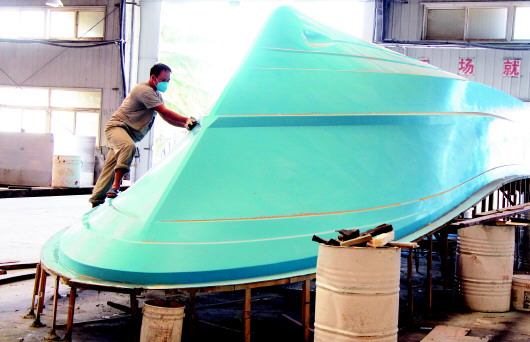
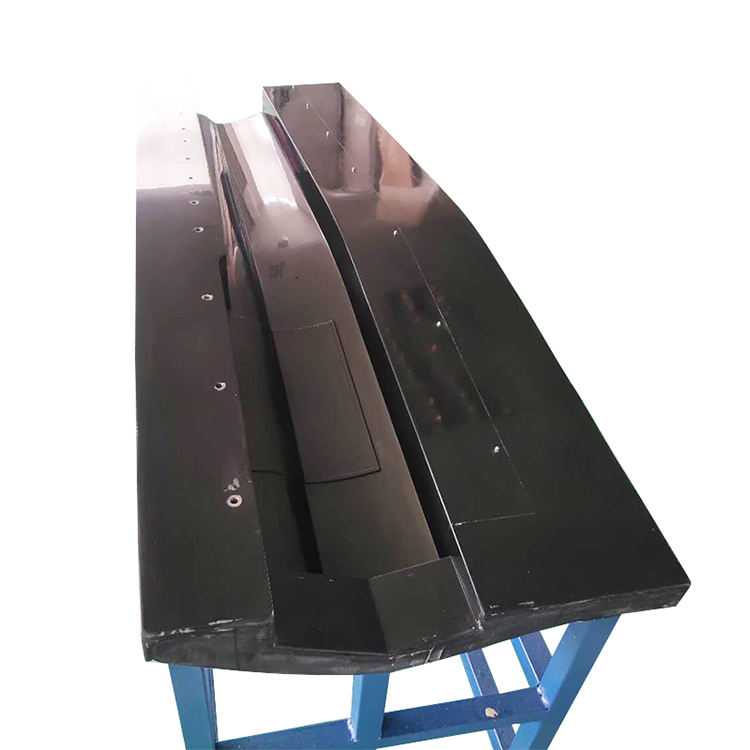
Composite tools are constructed with similar methods and materials as used in composites production. The cost of composites tools is considerably less than that of steel or aluminum molds. As an added benefit most composites shops have the technology and “know-how” to build composites tooling, whereas metal tooling usually has to be contracted to a tool and die manufacturer.
There is a range of methodology for the construction for composite tools, as well as many materials options. Quality tool building is critical to the quality of the part produced, and a significant level of expertise in tooling design and manufacturing is required. Based on internal tool building capability, the appropriate decision of in-house construction or outsourcing can be determined. The most often used materials associated with composites tool building are detailed below.
Sealing, Fairing, Priming and Surfacing Plugs and Patterns
-
Faring Compounds
-
Primers /Top Coatings
-
Surface Sealers
Open Mold Tooling
-
Tooling Gel Coats and Barrier Coats
-
Traditional Tooling Resins
-
Shrink Controlled Resins
-
Skin Coat Resins
Closed Mold Tooling (Light RTM, Vacuum Infusion, Reusable Bag Molding
-
B-Side or Upper Mold Gel Coats
-
Upper Mold Resins
-
Top Coat
Elevated Temperature Tooling
-
Epoxy Resins for Tooling
-
High Temp Coatings
-
High Temp Fairing and Priming
Repair and Refinishing
-
Reinforced Putties
-
Tooling Putties
-
Repair Resins with improved adhesion
-
Leveling Additives